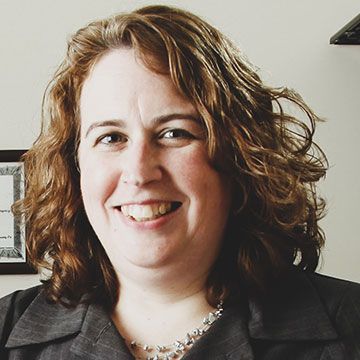
RECENT POSTS
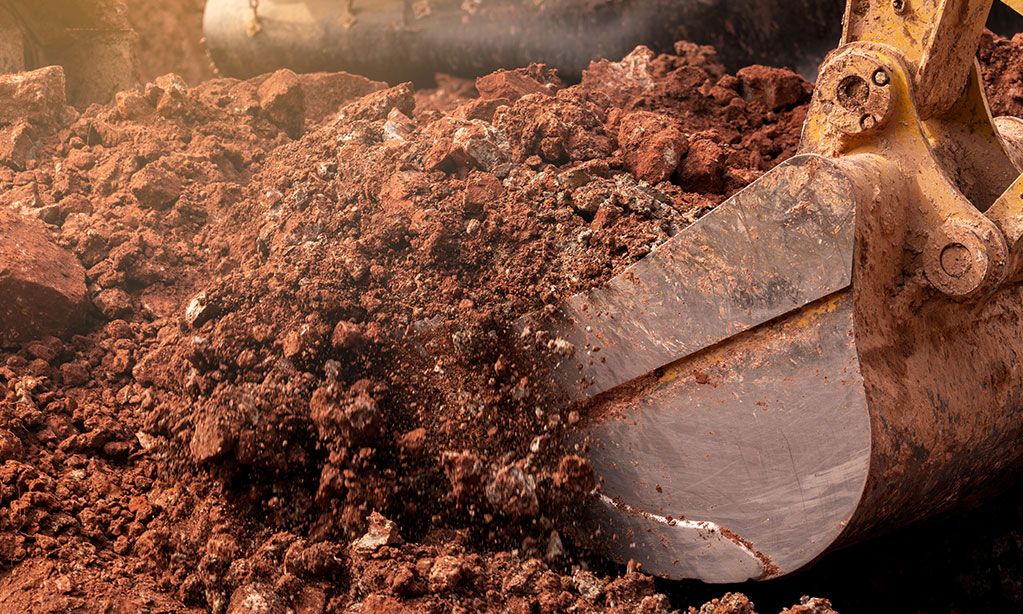
Five Construction General Permit (CGP) SWPPP Solutions
Five Construction General Permit (CGP) SWPPP Solutions
Technologies and Best Management Practices (BMPs) continually emerge and improve. This constant state of progress is a great thing when it comes to improving the quality of our nation’s waters. It’s also one of the reasons why the Clean Water Act (CWA) tasks the federal Environmental Protection Agency (EPA) with reviewing and renewing the National Pollutant Discharge Elimination System (NPDES) Construction General Permit (CGP) every five years.
Between permit cycles, EPA collects comments and proposals from various stakeholders, identifies changes and modifications to state permits, and reviews information from other sources when considering which permit clarifications and additions to propose and adopt for the next five-year cycle. In 2022, nine additions and 21 clarifications were made to the existing 2017 Construction General Permit (CGP).
The federal EPA issues NPDES permits in Massachusetts, New Hampshire, and New Mexico as well as US territories (except the Virgin Islands,) Puerto Rico, the District of Columbia, Tribal Lands, and for federal projects in certain states. In the other 47 states, permitting occurs at the state level.
Whether you’re getting ready to submit your next Notice of Intent (NOI) or looking for some new BMPs to strengthen your Stormwater Pollution Prevention Plan (SWPPP), focusing on these five areas can help you improve your operations and prevent pollutants from leaving your construction area.
1. Perimeter Controls
Perimeter controls provide the last line of defense against pollutants leaving a construction site. Most are engineered to capture dirt and silt. Some also capture trace oils and other contaminants. The most common types are silt fences, compost filter socks, gravel barriers, and temporary diversion dikes.
The 2022 Construction General Permit (CGP) clarified that sediment controls need to be installed upgradient of natural buffers, and along the perimeter of sites that are downslope from exposed soil or disturbed areas. (2022 CGP, Part 2.2.3)
Perimeter controls must also be effective. For example, stormwater cannot circumvent the edges of a control. Sediment must be removed before it accumulates to ½ of the height of the control device to prevent failure. Perimeter controls need to be inspected after storm events and repaired or replaced (if necessary) to prevent pollutants from being discharged. (2022 CGP, Part 2.2.3)
2. Drain Inlets
Storm drain inlets can be a great asset to keep rainwater and snowmelt from flooding your construction site after a storm. But unless the stormwater is directed to a sediment basin, sediment trap, or other control, the inlet must be protected. (Part 2.2.10, Part 7.2.4.g, Part 7.2.6.b.iv)
Without a sediment basin or similar control device, storm drain inlets are a direct path to receiving waters. Protecting inlets with devices that capture sediment and other pollutants helps to prevent plumes and sedimentation at outflows.
To remain effective, inlet protection controls need to be cleaned or removed and replaced when they become clogged or when sediment accumulates at the device’s inlet. Therefore, all inlet protection devices should be included in routine inspections as well as inspections after storm events, with sediment deposits being removed by the end of the business day that they are discovered. (Part 2.2.10)
3. Liquid Construction Product Wastes, Wash Water and Cleanout Waste
Concrete, paint, stucco, curing compounds, and form release oils are common construction wastes. When containers that previously held these compounds, or applicators that were used to apply these compounds are rinsed or washed, the wash water needs to be properly managed. (Part 2.3.4)
Properly managing wash water from cleaning applicators and containers includes:
- Locating washout and cleanout in designated areas that are as far as possible from storm drain inlets or receiving waters
- Directing wash water to an adequately-sized, leak-proof container or pit that prevents overflows and allows the water to be collected
- Preventing water from being dumped into storm inlets or receiving waters; or allowing it to infiltrate into soil
- Treating or disposing of the wash water in accordance with all applicable regulations
Hardened concrete waste should be collected and managed with other solid construction wastes.
4. Container Management
Properly managing containers not only prevents hazardous materials from entering the environment; but also ensures that each product will be available and ready for use when it is needed for the project. All containers that hold hazardous materials need to be kept closed when they are not in use to help prevent spills and hazardous air emissions. (Part 2.3.3, Part 7.2.6)
Product | Storage and Handling Requirements |
---|---|
Building materials and products |
|
Pesticides, herbicides, insecticides, fertilizers, and landscape materials |
|
Diesel fuel, oil, hydraulic fluids, other petroleum products, and other chemicals |
|
Hazardous or toxic wastes (paints, caulks, sealants, fluorescent light ballasts, solvents, wood preservatives, curing compounds, acids, etc.) |
|
Construction and domestic wastes (packaging materials, scrap, masonry products, timber, pipe and electrical cuttings, plastics, styrofoam, concrete, demolition debris; and other trash or discarded materials) |
|
Sanitary wastes |
|
5. Dewatering Operations
Dewatering includes draining accumulated stormwater and/or groundwater from foundations, vaults, trenches, or any other areas where it has accumulated. When these areas are drained, water pollutants – such as sediment and oil sheens – need to be contained onsite to prevent pollution.
The 2022 Construction General Permit (CGP) clarified and updated the requirements for dewatering operations. Inspections must take place each day there are dewatering activities. Operators must:
- Specify on the NOI that dewatering operations will be conducted
- Route water through a sediment control device
- Replace and clean filtering media on dewatering devices according to the manufacturer’s specifications
- Look for signs of visual turbidity such as cloudiness, opaqueness, or water that has a visible contrast to receiving waters during inspections
- Prohibit discharges containing visible floating solids, foam, or oil sheens
- Allow dewatering water to infiltrate in well-vegetated, erosion-resistant, upland areas whenever possible
- Prohibit the use of receiving waters as part of the treatment area
- Haul away backwash water or return it to the beginning of the treatment process
- Keep records of inspections, including photographs
Preparing for Construction General Permit Updates
Regularly reviewing the BMPs listed in SWPPPs, and upgrading them to reflect newer, more effective technologies can help operators prepare for new requirements in each EPA permit cycle and assure that they’re doing their part to prevent pollution.
Shop SWPPP Solutions
Related Articles
TALK TO AN EXPERT
If you have a question about the 2022 Construction General Permit (CGP), we’re here to help. Our team can address your questions and assist in implementing changes to your SWPPP. Call 814-822-2004 or email sales@halenhardy.com.