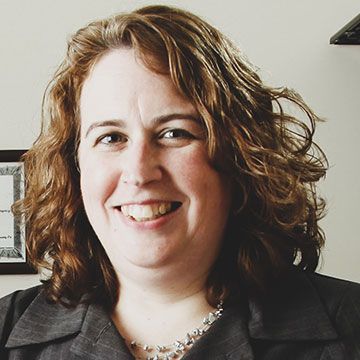
RECENT POSTS
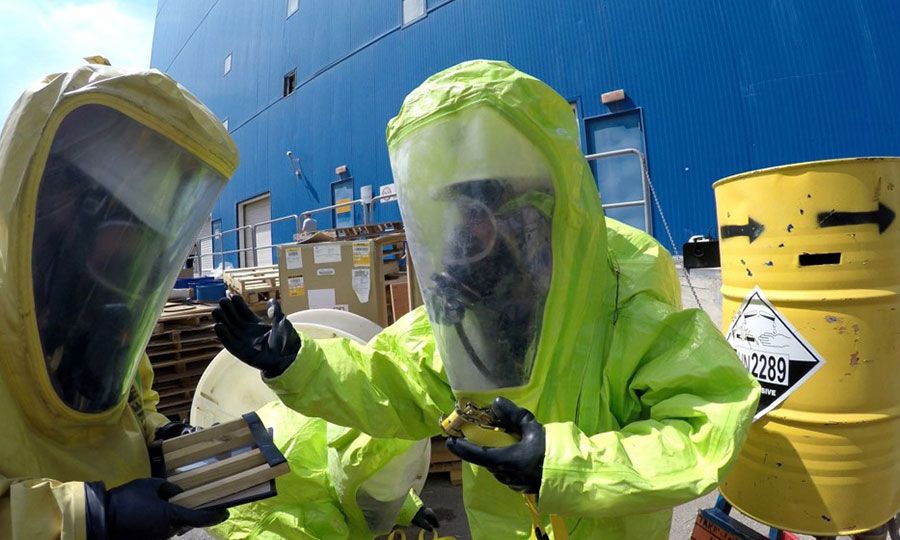
Process Safety Management (PSM) Overview 29 CFR 1910.119
Process Safety Management is one of the two key rules that came out of the requirements of section 112(r) of the Clean Air Act. [The other is EPA’s Risk Management Plan (RMP) Rule.] Owners and operators of facilities that manufacture, use, store or otherwise process more than a threshold quantity of flammable liquids (except flammable fuels that are used as fuel) or any of the 130 toxic substances found in 29 CFR 1910.119, Appendix A are subject to this rule.
The PSM rule focuses on performing process hazard analysis (PHA) for all processes involving highly hazardous chemicals to determine what may go wrong, and implementing safeguards to prevent or reduce the risks. Plans must include at least the following elements:
-
Process Safety Information – identifies the hazards presented by chemicals processed onsite as well as the equipment used and any technologies incorporated.
-
Process Hazard Analysis (PHA) – evaluates human factors, engineering and administrative controls and consequences of accidental chemical releases from processes.
-
Operating Procedures – develops clear, accurate instructions for startup, normal operations, emergency shutdowns, etc. that can be followed by employees operating processes.
-
Non-Routine Work Authorization – development of plans, procedures and training for non-routine work, such as hot work, confined space entry, etc.
-
Employee Participation – involving employees in the development of PHAs and providing access to plans.
-
Pre-Startup Safety Review – establishes processes for confirming that new or changed equipment or procedures will not affect current processes or create new hazards.
-
Mechanical Integrity of Equipment – establishes schedules for inspecting, testing and maintaining processing equipment.
-
Training – teaches employees to recognize hazards, follow established procedures and know what to do when emergencies arise.
-
Contractors – coordinates training, plans and processes with outside workforces to ensure safety of both employees and the outside workforce.
-
Management of Change – evaluates changes to process chemicals, technology, equipment, and procedures.
-
Incident Investigation – reviews incidents and near misses to determine root causes so that plans can be amended to avoid the event in the future.
-
Emergency Preparedness, Planning and Response – creates and implements an Emergency Action Plan (EAP) that outlines specific actions that employees will take when there is a chemical release.
-
Compliance Audits – verifies that the procedures outlined in the plan are still appropriate, accurate and being followed.
Subscribe for Updates:
Sign up here to get the latest news, rules, and regulations and delivered right to your inbox.