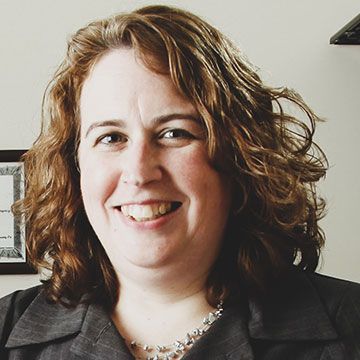
RECENT POSTS
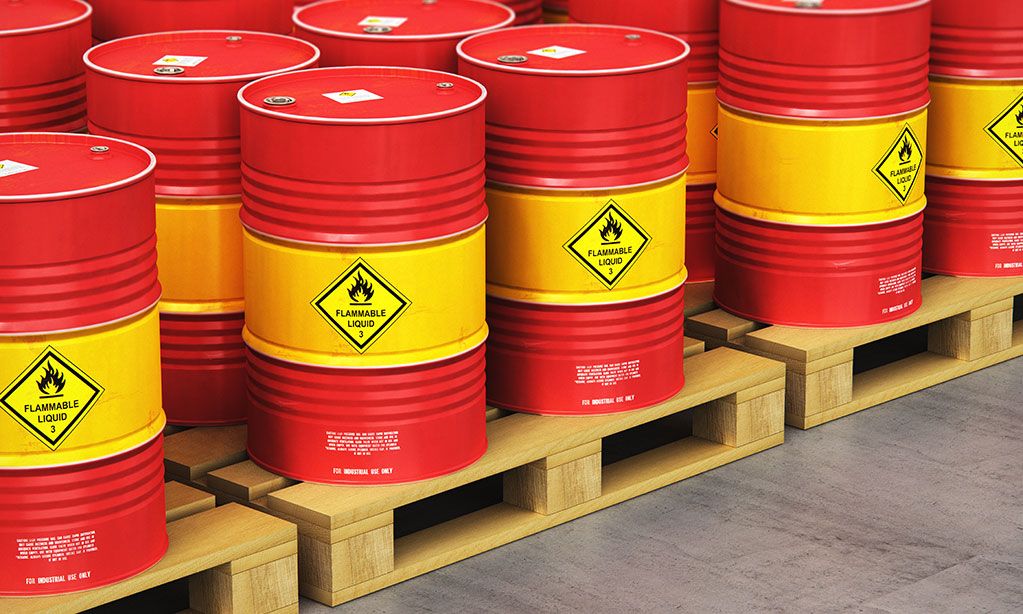
Risk Management Plans
Risk Management Plans (RMPs) were one of the two key rules that came out of the requirements of section 112(r) of the Clean Air Act. [The other is OSHA’s Process Safety Management (PSM) Rule.] Owners and operators of facilities that manufacture, use, store or otherwise process more than a threshold quantity of flammable liquids (except flammable fuels that are used as fuel) or any of the 140 toxic substances found in 40 CFR 68.130 are subject to this rule. These facilities must:
-
Perform a hazard assessment for each threshold quantity hazardous chemical and process
-
Establish a program that outlines safe operational procedures to prevent accidental chemical releases and process failures
-
Explore worse case scenarios and create an emergency response program to mitigates risk
-
Share plans with local responders and conduct training for employees
Each chemical and process subject to the Plan must be grouped into one of the program’s three eligibility levels.
-
Program 1:
No releases in the past 5 years; no release that could affect the public; plans coordinated with local responders
-
Program 2:
Anyone that doesn’t fit in Program 1 or 3
-
Program 3:
Facility is subject to OSHA’s PSM rule; or is in a designated NAICS code (pulp mills, petroleum refineries, petrochemical mfg, alkali and chlorine mfg, inorganic chemical mfg, organic chemical mfg, cycling crude and intermediate mfg, plastic material and resin mfg, nitrogenous fertilizer mfg, pesticide and agricultural chemical mfg)
Each eligibility level has specific requirements, with Program 1 having fewer than Program 3. However, all chemicals and processes are collectively managed with one plan, regardless of their individual eligibility level(s). Most facilities that have chemicals and processes in multiple levels choose to manage all chemicals and processes as if they are in the most stringent level to simplify training.
Plans must specify whether onsite employees will respond to spills or if employees will evacuate and outside contractors will be utilized. With either option, facilities must be able to demonstrate that they have appropriate processes, procedures and equipment in place to handle a worst-case scenario spill.
Subscribe for Updates:
Sign up here to get the latest news, rules, and regulations and delivered right to your inbox.